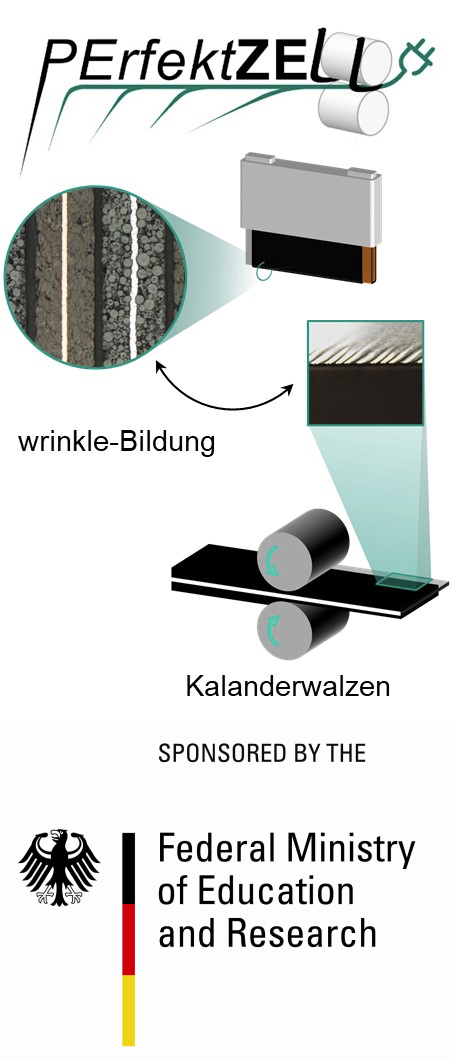
PErfektZELL - Process Quality Improvement for Cell Production
- Contact:
Benjamin Bold
- Project Group:
- Funding:
- Partner:
Varta Microbattery GmbH
Hochschule Aalen - Institut für Materialforschung
BREYER GmbH Maschinenfabrik
Assoziierte Partner: BMW AG, Hydro Aluminium Deutschland GmbH, GOM GmbH
- Startdate:
01.01.2019
- Enddate:
31.12.2021
Objectives and Results
Electric mobility is a central topic for Germany. The development of the German economy depends very much on battery activities. On the one hand, further development of the material systems is necessary and on the other hand, progress is needed in production. Both aspects influence the energy density of the battery cell and thus determine the range of electrically powered vehicles.
The achievement of a high energy density can be achieved on the one hand by the material composition and on the other hand can be influenced by the manufacturing process. The first step is to identify the cause of the wrinkling. This forms the basis for designing and building an additional module on the calender within the project, so that wrinkle-free processing of current and future material systems is possible. Consequently, a higher compaction and energy density is possible.
Contents and Approach
The decisive process step is calendering, in which the volumetric energy density is increased by compressing the active material. The preforms introduced into the material lead to the formation of wrinkles at the high required densities of cathode materials. This leads to problems in the further process steps and thus prevents the maximum possible compaction. An image processing system is set up to detect the distortion of the electrode during calendering. The resulting measured variable, the strain difference between the coated and uncoated area, is coupled with further investigations on the material to build up the process understanding.
This allows the requirements to be set for the avoidance module, which is implemented on the calender for crease-free processing. Finally, battery cells will be built to validate the higher energy density.
Project Volume
1,3 Mio. €